Glassware washers play a vital role in pharmaceutical companies and are mainly used for efficient cleaning and sterilization of glassware in laboratories, production plants, etc., to ensure compliance, safety, and reproducibility of results in experimental and production processes. Below are its specific applications and importance:
Application Scenarios
1. Quality Control (QC) Laboratory

Purpose: To clean glassware for testing (e.g. volumetric flasks, pipettes, cuvettes, chromatography injection bottles, etc.).
Importance: Avoid residues interfering with test results (e.g. HPLC, UV testing) and ensure data accuracy.
Comply with the mandatory requirements of GMP/GLP on the cleanliness of labware.
2. Research and Development Laboratory (R&D)
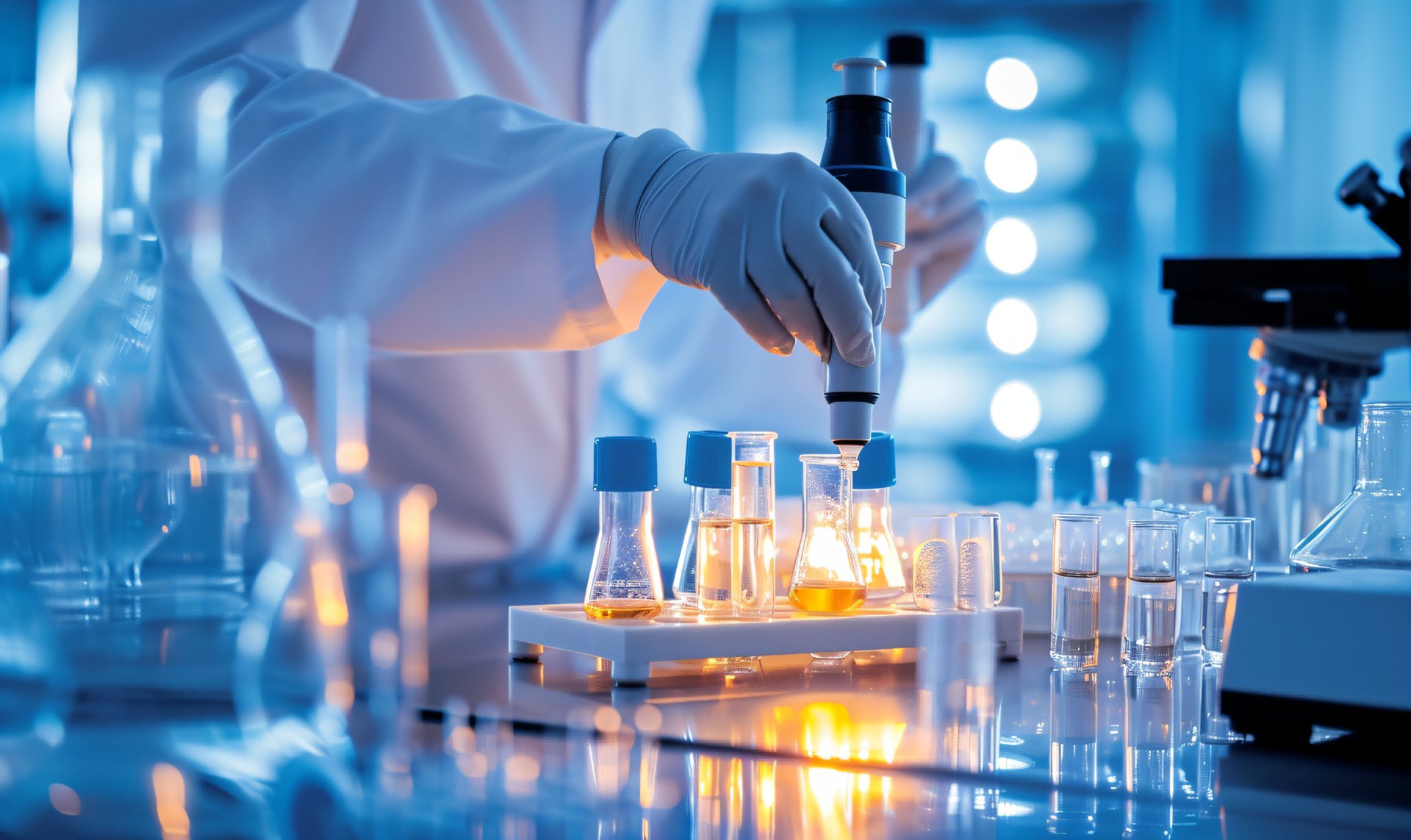
Purpose: To clean experimental beakers, conical flasks, Petri dishes, reaction kettles, etc.
Importance: Ensure the reproducibility of experiments, especially the stability test of formulations in the development of new drugs.
Reduce the impact of chemical residues on the experimental results (such as catalyst residues interfere with the reaction).
3. Aseptic preparation production area
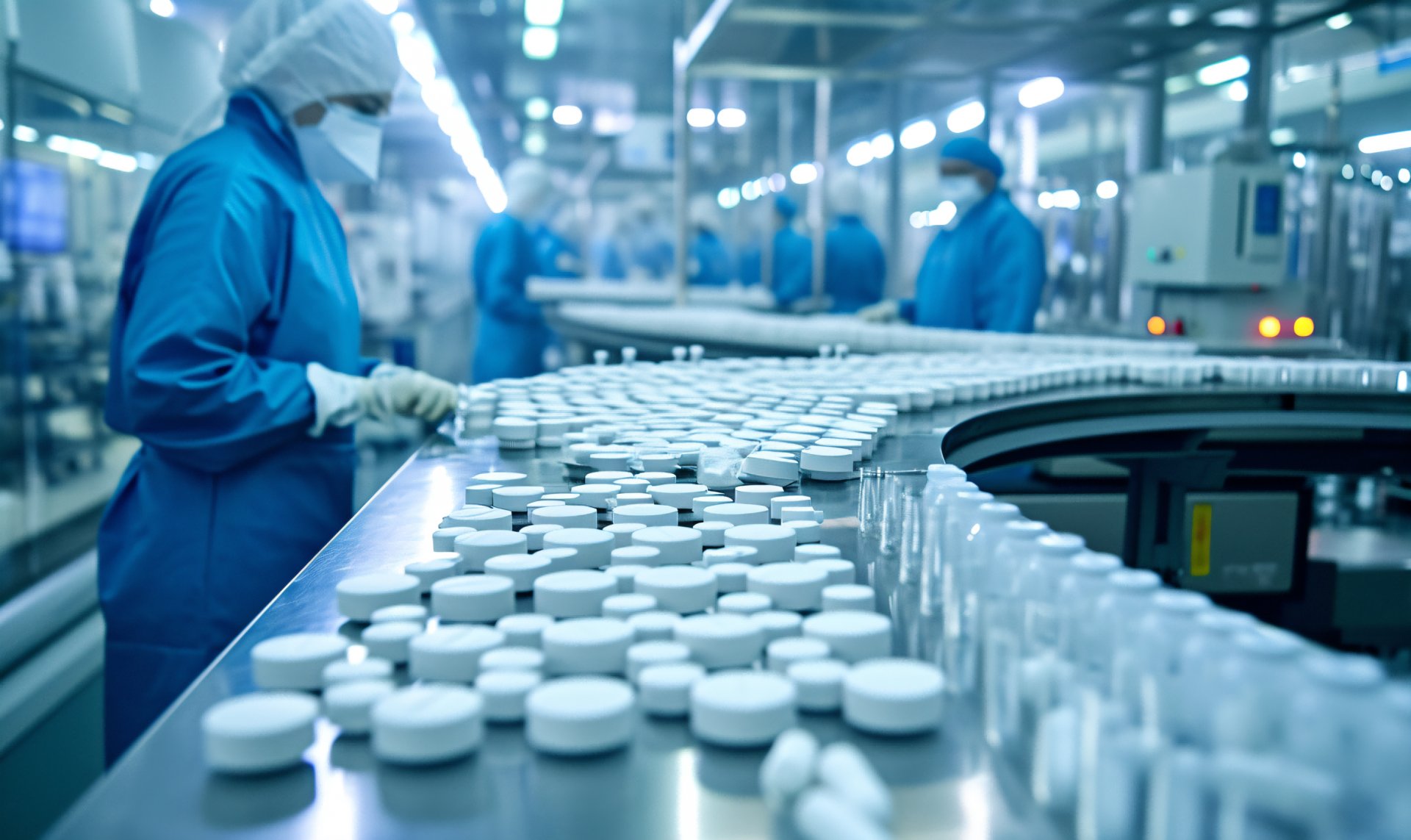
Purpose: Cleaning of glass parts in direct contact with pharmaceutical products (e.g. dispensing tanks, storage bottles, filling line components).
Key requirements:
Depyrogenation: high temperature (e.g. above 250°C) or acid-base treatment is required to remove endotoxins (necessary for injectable production).
Sterilization linkage: some washers have integrated steam sterilization (SIP) functionality, directly into the aseptic filling process,we also offer horizontal sterilizer suitable for GMP level sterilization.
Core Functions and Advantages
Highly efficient decontamination
Removal of stubborn residues (e.g. proteins, lipids, chemical reagents) by high-temperature spraying, ultrasonic cleaning, or chemical detergents (e.g., water for injection, acid/alkaline solution).
Standardized Processes
Preset cleaning programs (time, temperature, spray pressure) meet GMP (Good Manufacturing Practice) requirements and reduce manual handling variations.
Sterilization and Depyrogenation
Some equipment integrates high-temperature drying or steam sterilization to remove endotoxins (pyrogens), which is key for injectable production. We also offer high-temperature drying ovens suitable for de-heating sources.
Validation & Traceability
Supports cleaning data logging (e.g. temperature, time, pressure) for easy validation (IQ/OQ/PQ) and audit trail.

In pharmaceutical factories, glassware washers are not only a cleaning tool, but also an important part of ensuring the quality and safety of medicines. The standardized, traceable cleaning process reduces the risk of contamination and meets stringent regulatory requirements, especially in the production of high-risk preparations (e.g., sterile preparations, biologics). Compliance, efficiency and compatibility with existing production lines need to be taken into account when selecting the right machine.